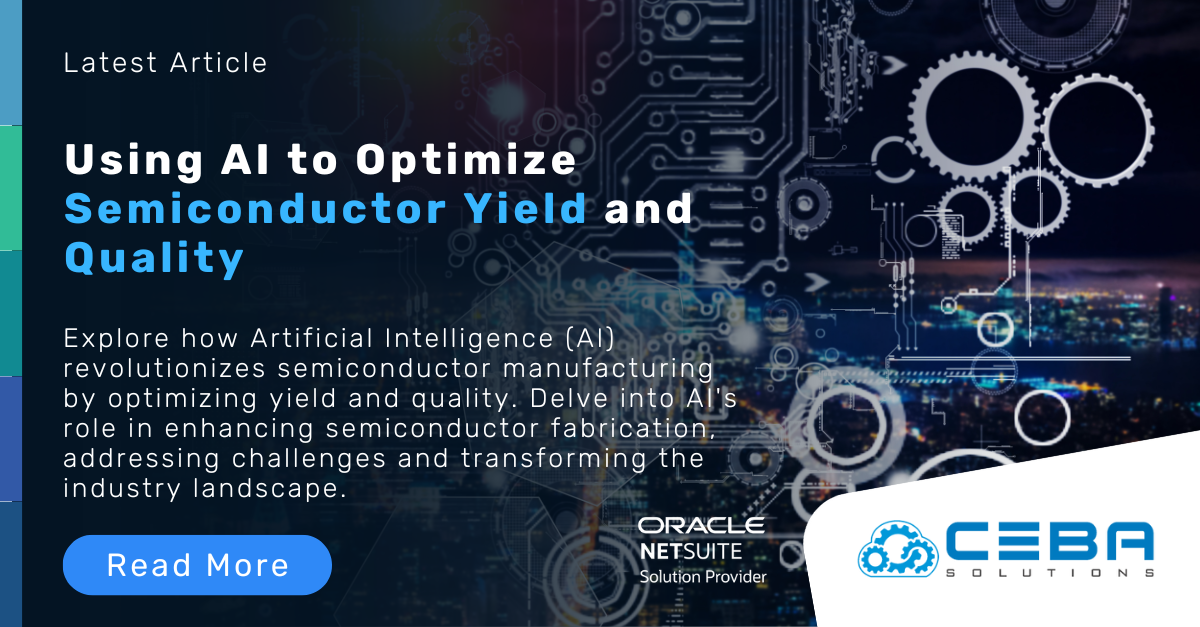
Using AI to Optimize Semiconductor Yield and Quality
Using AI to Optimize Semiconductor Yield and Quality
The semiconductor industry is a cornerstone of modern technology, powering everything from smartphones and computers to advanced medical devices and automobiles. Ensuring high yield and quality in semiconductor manufacturing is critical, as even minor defects can lead to significant performance issues or failures in electronic devices. As the complexity of semiconductor devices increases, traditional methods of quality control and yield optimization face significant challenges. Enter artificial intelligence (AI), which offers transformative solutions for optimizing semiconductor yield and quality. This article explores how AI is being used to enhance semiconductor manufacturing processes, the benefits it brings, and implementation strategies.
The Challenges in Semiconductor Manufacturing
- Complexity of Processes: Semiconductor manufacturing involves multiple intricate steps, including wafer fabrication, lithography, etching, doping, and packaging. Each step must be meticulously controlled to ensure high yield and quality.
- Microscopic Defects: Defects in semiconductor manufacturing can be microscopic and difficult to detect with traditional methods, yet they can significantly impact device performance.
- Data Overload: The manufacturing process generates massive amounts of data, which can be overwhelming to analyze and utilize effectively without advanced tools.
- Yield Variability: Variability in yield can result from numerous factors, including material inconsistencies, equipment variations, and process deviations. Managing this variability is crucial for maintaining profitability and product reliability.
How AI Optimizes Semiconductor Yield and Quality
AI leverages machine learning algorithms, predictive analytics, and big data to address the complexities and challenges in semiconductor manufacturing. Here are some key ways AI is optimizing yield and quality:
- Predictive Maintenance and Equipment Optimization
- Anomaly Detection: AI algorithms analyze data from manufacturing equipment to detect anomalies and predict potential failures before they occur. This proactive approach minimizes downtime and ensures that equipment operates optimally.
- Maintenance Scheduling: Predictive analytics help schedule maintenance activities based on equipment condition rather than fixed intervals, reducing unnecessary maintenance and prolonging equipment life.
- Defect Detection and Classification
- Computer Vision: AI-powered computer vision systems inspect wafers and semiconductor devices for defects with high precision. These systems can identify microscopic defects that are difficult to detect with traditional inspection methods.
- Automated Classification: Machine learning algorithms classify defects based on their characteristics, helping engineers understand defect types and root causes. This information is crucial for implementing corrective actions.
- Process Optimization
- Real-Time Process Control: AI enables real-time monitoring and control of manufacturing processes. By continuously analyzing process data, AI can adjust parameters to maintain optimal conditions and improve yield.
- Process Modeling: Machine learning models simulate various manufacturing scenarios to identify the best process parameters and conditions. This helps optimize process settings and reduce variability.
- Yield Prediction and Enhancement
- Yield Prediction Models: AI models predict yield outcomes based on historical data and current process conditions. These predictions help manufacturers anticipate yield issues and take preemptive measures.
- Root Cause Analysis: AI analyzes yield data to identify patterns and correlations that indicate potential causes of yield loss. This deep understanding allows for targeted improvements in the manufacturing process.
- Supply Chain Optimization
- Material Quality Monitoring: AI monitors the quality of materials used in semiconductor manufacturing, ensuring that only high-quality materials are utilized. This reduces the risk of defects related to material inconsistencies.
- Supplier Performance Analysis: AI evaluates supplier performance based on historical data, helping manufacturers select reliable suppliers and maintain high material quality standards.
Benefits of AI-Driven Yield and Quality Optimization
- Increased Yield: AI-driven optimization improves overall yield by identifying and mitigating factors that cause defects and variability in the manufacturing process.
- Enhanced Quality: By detecting and addressing defects early, AI ensures that semiconductor devices meet stringent quality standards, reducing the likelihood of failures in the field.
- Cost Savings: Improved yield and quality translate to lower production costs, as fewer resources are wasted on defective products and rework.
- Reduced Downtime: Predictive maintenance and real-time process control minimize equipment downtime, ensuring smooth and continuous production.
- Data-Driven Decisions: AI provides actionable insights based on comprehensive data analysis, enabling informed decision-making and strategic process improvements.
Implementing AI in Semiconductor Manufacturing
- Data Integration and Management
- Comprehensive Data Collection: Collect data from all stages of the manufacturing process, including equipment performance, process parameters, and defect inspection results.
- Data Quality: Ensure that collected data is accurate, complete, and consistent. High-quality data is essential for effective AI model training and analysis.
- Building and Training AI Models
- Selecting Algorithms: Choose appropriate machine learning algorithms for tasks such as anomaly detection, defect classification, and yield prediction. Common algorithms include neural networks, support vector machines, and decision trees.
- Model Training: Train AI models using historical data and continuously update them with new data to improve accuracy and adaptability.
- Integrating AI with Existing Systems
- Seamless Integration: Integrate AI solutions with existing manufacturing execution systems (MES), enterprise resource planning (ERP) systems, and other relevant platforms to ensure smooth data flow and process integration.
- Collaboration with Vendors: Work with AI technology vendors to customize solutions that meet specific manufacturing needs and challenges.
- Employee Training and Support
- Skill Development: Provide training for engineers and operators to understand and effectively use AI tools and insights. Emphasize the importance of data-driven decision-making.
- Ongoing Support: Offer ongoing technical support and resources to help employees troubleshoot issues and optimize the use of AI solutions.
- Continuous Improvement and Monitoring
- Performance Metrics: Establish key performance indicators (KPIs) to monitor the effectiveness of AI-driven optimization efforts. Common KPIs include yield rates, defect rates, and equipment uptime.
- Regular Reviews: Conduct regular reviews of AI model performance and process outcomes to identify areas for further improvement and refinement.
Challenges and Considerations
- Data Privacy and Security
- Protecting Sensitive Data: Implement robust data security measures to protect sensitive manufacturing data from unauthorized access and breaches.
- Compliance: Ensure compliance with industry regulations and standards regarding data privacy and security.
- Initial Costs and ROI
- Upfront Investment: Be prepared for the initial costs associated with implementing AI solutions, including hardware, software, and training.
- Long-Term ROI: Focus on the long-term return on investment, considering the cost savings, yield improvements, and quality enhancements that AI can deliver.
- Change Management
- Adoption and Acceptance: Foster a culture of innovation and encourage acceptance of AI-driven solutions among employees. Highlight the benefits and provide support during the transition.
Conclusion
AI-driven quality assurance and yield optimization are revolutionizing the semiconductor manufacturing industry. By leveraging advanced machine learning algorithms, computer vision, and big data analytics, manufacturers can achieve higher yield, enhanced quality, and significant cost savings. Implementing AI solutions requires careful planning, data integration, and employee training, but the benefits far outweigh the challenges. As AI technology continues to evolve, its impact on semiconductor manufacturing will only grow, driving innovation and excellence in the industry. Embracing AI is not just a competitive advantage but a necessary step toward the future of semiconductor manufacturing.