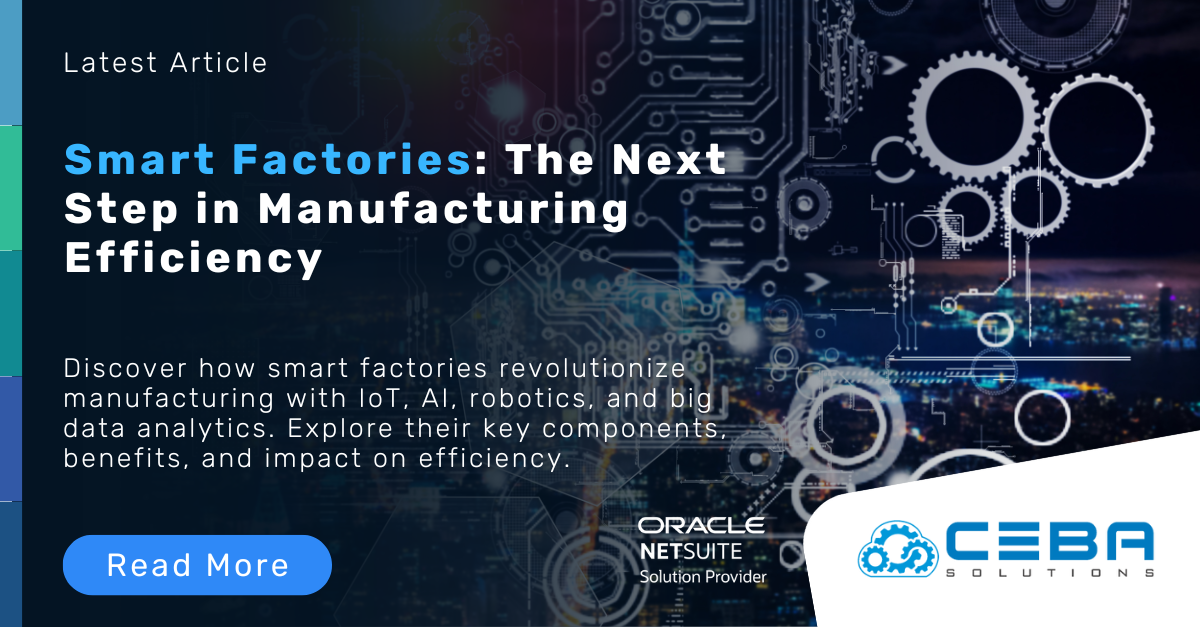
Smart Factories: The Next Step in Manufacturing Efficiency
Smart Factories: The Next Step in Manufacturing Efficiency
In the rapidly evolving world of manufacturing, efficiency, agility, and innovation are paramount. As industries strive to meet growing demands and complex production challenges, the concept of smart factories has emerged as a transformative force. Smart factories leverage advanced technologies such as the Internet of Things (IoT), artificial intelligence (AI), big data analytics, and robotics to create highly automated and connected manufacturing environments. This article explores the next step in manufacturing efficiency through the development and implementation of smart factories, highlighting their benefits, key technologies, and strategies for successful adoption.
Understanding Smart Factories
A smart factory is a highly digitized and connected production facility that relies on advanced technologies to enhance manufacturing processes. These factories integrate cyber-physical systems, IoT devices, and AI to enable real-time monitoring, autonomous decision-making, and seamless communication across the production line. The ultimate goal is to create a responsive, adaptive, and efficient manufacturing environment that can optimize performance, reduce downtime, and improve product quality.
Key Technologies Driving Smart Factories
- Internet of Things (IoT)
- Connected Devices: IoT enables the interconnection of machines, sensors, and devices within the factory. These connected devices collect and share data in real-time, providing valuable insights into equipment performance, environmental conditions, and production metrics.
- Real-Time Monitoring: IoT facilitates real-time monitoring of production processes, allowing for immediate detection of anomalies and swift corrective actions.
- Artificial Intelligence (AI) and Machine Learning
- Predictive Maintenance: AI-powered predictive maintenance uses machine learning algorithms to analyze data from equipment sensors, predict potential failures, and schedule maintenance proactively. This reduces unplanned downtime and extends equipment lifespan.
- Process Optimization: AI algorithms optimize manufacturing processes by analyzing production data, identifying inefficiencies, and recommending improvements. This leads to increased productivity and reduced waste.
- Big Data Analytics
- Data Integration and Analysis: Big data analytics integrates data from various sources, including IoT devices, enterprise systems, and supply chain networks. Advanced analytics tools process and analyze this data to generate actionable insights.
- Informed Decision-Making: Data-driven insights enable informed decision-making, helping manufacturers optimize production schedules, inventory management, and resource allocation.
- Robotics and Automation
- Collaborative Robots (Cobots): Cobots work alongside human operators, assisting with tasks that require precision, strength, or repetitive actions. They enhance productivity and improve workplace safety.
- Automated Guided Vehicles (AGVs): AGVs automate material handling and transportation within the factory, ensuring timely delivery of components and reducing manual labor.
- Digital Twins
- Virtual Replicas: Digital twins are virtual replicas of physical assets, processes, or systems. They simulate real-world conditions, allowing manufacturers to monitor performance, test scenarios, and optimize operations without disrupting actual production.
- Predictive Analysis: Digital twins use real-time data to predict potential issues and assess the impact of changes before implementation.
Benefits of Smart Factories
- Increased Efficiency and Productivity
- Optimized Processes: Advanced technologies streamline production processes, reducing cycle times and increasing output. Automated systems minimize human error and ensure consistent quality.
- Resource Optimization: Smart factories optimize the use of resources, including materials, energy, and labor. This reduces waste and lowers operational costs.
- Enhanced Quality and Consistency
- Real-Time Quality Control: Continuous monitoring and analysis of production data ensure that products meet high-quality standards. Immediate detection of defects allows for quick corrections, minimizing rework and scrap.
- Data-Driven Insights: AI and analytics provide insights into quality trends, enabling manufacturers to implement continuous improvement initiatives.
- Reduced Downtime and Maintenance Costs
- Predictive Maintenance: Proactive maintenance based on AI predictions reduces unplanned downtime and prevents costly equipment failures. This extends the lifespan of machinery and lowers maintenance expenses.
- Swift Issue Resolution: Real-time monitoring and diagnostics enable rapid identification and resolution of production issues, keeping the factory running smoothly.
- Improved Flexibility and Agility
- Agile Production: Smart factories can quickly adapt to changes in demand, product variations, and market conditions. Flexible manufacturing systems allow for rapid reconfiguration and scaling.
- Customization and Personalization: Advanced technologies enable the efficient production of customized and personalized products, meeting specific customer requirements.
- Enhanced Safety and Sustainability
- Workplace Safety: Automation and robotics reduce the need for manual labor in hazardous environments, enhancing worker safety. Real-time monitoring ensures compliance with safety protocols.
- Sustainable Practices: Smart factories optimize energy consumption, reduce waste, and promote sustainable manufacturing practices. This minimizes environmental impact and supports corporate sustainability goals.
Implementing Smart Factories: Strategies for Success
- Comprehensive Assessment and Planning
- Needs Assessment: Conduct a thorough assessment of current manufacturing processes, identifying areas for improvement and potential benefits of smart factory technologies.
- Strategic Planning: Develop a detailed implementation plan, outlining objectives, timelines, and resource requirements. Ensure alignment with overall business goals and stakeholder buy-in.
- Investment in Technology and Infrastructure
- Technology Selection: Choose appropriate technologies based on specific manufacturing needs. Consider factors such as scalability, compatibility, and ease of integration.
- Infrastructure Development: Invest in the necessary infrastructure, including high-speed data networks, cloud computing, and IoT platforms. Ensure robust cybersecurity measures to protect data and systems.
- Data Integration and Management
- Unified Data Platform: Implement a unified data platform that integrates data from various sources, enabling seamless data flow and comprehensive analysis.
- Data Governance: Establish data governance policies to ensure data accuracy, consistency, and security. Define roles and responsibilities for data management.
- Employee Training and Change Management
- Skill Development: Provide training programs to equip employees with the skills needed to operate and maintain smart factory technologies. Emphasize the importance of data-driven decision-making.
- Change Management: Implement change management strategies to facilitate smooth adoption of new technologies. Address any resistance and highlight the benefits of smart factories.
- Continuous Improvement and Innovation
- Performance Monitoring: Continuously monitor the performance of smart factory systems, using key performance indicators (KPIs) to track progress and identify areas for improvement.
- Innovation Culture: Foster a culture of innovation, encouraging employees to contribute ideas for optimizing processes and implementing new technologies.
Conclusion
Smart factories represent the next step in manufacturing efficiency, offering a transformative approach to production that leverages advanced technologies to optimize processes, enhance quality, and improve agility. By integrating IoT, AI, big data analytics, and robotics, smart factories enable real-time monitoring, predictive maintenance, and data-driven decision-making, leading to significant benefits for manufacturers. Implementing smart factory solutions requires careful planning, investment in technology and infrastructure, and a focus on employee training and change management. As industries continue to evolve, smart factories will play a crucial role in driving innovation, sustainability, and competitiveness in the manufacturing sector.