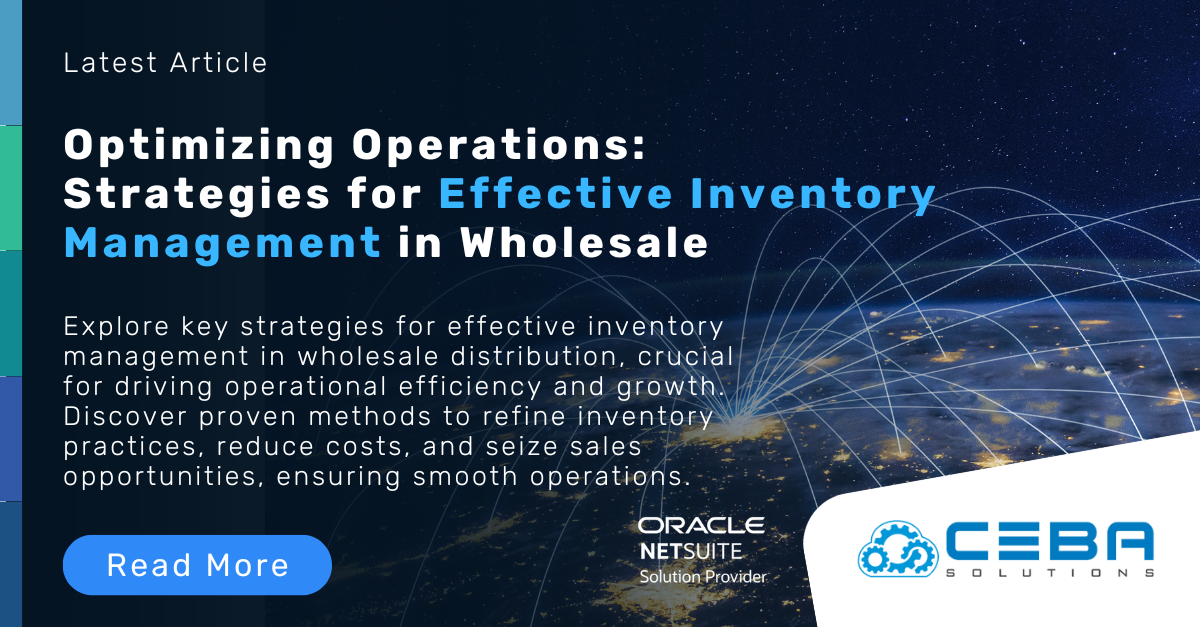
Optimizing Operations: Strategies for Effective Inventory Management in Wholesale
Optimizing Operations: Strategies for Effective Inventory Management in Wholesale
Effective inventory management is crucial for wholesalers to maintain smooth operations, meet customer demands, and optimize costs. As the backbone of wholesale distribution, inventory management involves the efficient tracking, ordering, and storing of products. With the increasing complexity of supply chains and the growing demands of customers, wholesalers must adopt advanced strategies to optimize their inventory management processes. This article explores key strategies for effective inventory management in wholesale, highlighting the benefits of optimized operations and practical implementation steps.
The Importance of Effective Inventory Management
- Customer Satisfaction: Ensuring that products are available when customers need them enhances satisfaction and loyalty.
- Cost Efficiency: Reducing excess inventory and minimizing stockouts lowers holding costs and avoids lost sales.
- Operational Efficiency: Streamlined inventory processes improve overall operational efficiency and reduce waste.
- Profitability: Effective inventory management helps maintain healthy profit margins by balancing supply and demand.
Key Strategies for Effective Inventory Management
- Demand Forecasting
- Predictive Analytics: Use predictive analytics to forecast demand based on historical sales data, market trends, and seasonal patterns. Accurate demand forecasting helps maintain optimal inventory levels.
- Real-Time Data: Leverage real-time data to adjust forecasts dynamically. This ensures that inventory levels align with current market conditions and customer demands.
- Inventory Optimization Techniques
- ABC Analysis: Categorize inventory items into three groups (A, B, and C) based on their importance and value. Focus on managing 'A' items closely as they contribute the most to revenue, while 'B' and 'C' items can be managed with less intensity.
- Safety Stock: Determine the appropriate level of safety stock to buffer against demand variability and supply chain disruptions. Safety stock ensures that critical items are always available.
- Just-In-Time (JIT) Inventory
- Minimize Holding Costs: Implement JIT inventory management to reduce holding costs by receiving goods only when they are needed for production or sales. This minimizes excess inventory and frees up capital.
- Supplier Collaboration: Establish strong relationships with reliable suppliers to ensure timely deliveries and reduce lead times. Effective supplier collaboration is crucial for the success of JIT inventory.
- Automated Inventory Management Systems
- Inventory Management Software: Invest in advanced inventory management software to automate tracking, ordering, and reporting processes. These systems provide real-time visibility into inventory levels and streamline operations.
- Barcode and RFID Technology: Use barcode scanning and RFID technology to improve accuracy in inventory tracking and reduce manual errors. These technologies enhance efficiency in inventory management.
- Cross-Docking
- Streamline Distribution: Implement cross-docking to move products directly from receiving to shipping, bypassing storage. This reduces handling time, minimizes storage costs, and accelerates the distribution process.
- Efficient Sorting: Use sorting systems to quickly allocate incoming products to their final destinations. Efficient sorting ensures that products reach customers faster.
- Regular Audits and Cycle Counting
- Inventory Audits: Conduct regular inventory audits to verify stock levels and identify discrepancies. Audits help maintain accuracy and ensure that records match physical inventory.
- Cycle Counting: Implement cycle counting to continuously count small portions of inventory on a rotating basis. This method reduces the need for full inventory counts and helps identify issues early.
- Lean Inventory Practices
- Reduce Waste: Adopt lean inventory practices to eliminate waste and improve efficiency. Focus on minimizing excess inventory, reducing lead times, and optimizing storage space.
- Continuous Improvement: Encourage a culture of continuous improvement by regularly reviewing and refining inventory management processes. Involve employees in identifying inefficiencies and implementing solutions.
Benefits of Optimized Inventory Management
- Cost Savings
- Reduced Holding Costs: Optimized inventory levels reduce the costs associated with storing excess inventory, such as warehousing, insurance, and obsolescence.
- Lower Order Costs: Efficient inventory management reduces the frequency and cost of emergency orders and stockouts, resulting in cost savings.
- Enhanced Customer Satisfaction
- Product Availability: Ensuring that products are consistently available improves customer satisfaction and reduces the risk of lost sales.
- Timely Deliveries: Efficient inventory management enables timely order fulfillment, enhancing customer trust and loyalty.
- Improved Cash Flow
- Freed-Up Capital: Reducing excess inventory frees up capital that can be invested in other areas of the business, such as marketing, expansion, or product development.
- Better Financial Planning: Accurate demand forecasting and inventory optimization improve financial planning and budgeting.
- Operational Efficiency
- Streamlined Processes: Automated and efficient inventory management processes reduce manual effort, improve accuracy, and enhance overall operational efficiency.
- Reduced Waste: Lean inventory practices minimize waste, optimize storage space, and improve resource utilization.
Implementing Effective Inventory Management
- Assess Current Processes
- Evaluate Systems: Assess your current inventory management systems and processes to identify areas for improvement. Look for inefficiencies, inaccuracies, and bottlenecks.
- Set Goals: Define clear goals for inventory management, such as reducing holding costs, improving accuracy, or increasing customer satisfaction.
- Choose the Right Technology
- Select Software: Choose inventory management software that meets your business needs and integrates with your existing systems. Look for features such as real-time tracking, automated ordering, and advanced analytics.
- Implement Technology: Implement barcode scanning, RFID technology, and other tools to enhance accuracy and efficiency in inventory management.
- Train Employees
- Provide Training: Train employees on new inventory management systems and processes. Ensure they understand the importance of accurate inventory tracking and how to use the tools effectively.
- Encourage Adoption: Foster a culture that embraces technology and continuous improvement. Encourage employees to provide feedback and suggest improvements.
- Monitor and Adjust
- Track Performance: Use key performance indicators (KPIs) to monitor the performance of your inventory management processes. Common KPIs include inventory turnover, order accuracy, and carrying costs.
- Continuous Improvement: Regularly review performance data and make adjustments to optimize inventory management. Stay flexible and responsive to changes in market conditions and customer demands.
Conclusion
Effective inventory management is essential for wholesalers to optimize operations, reduce costs, and enhance customer satisfaction. By adopting strategies such as demand forecasting, inventory optimization, just-in-time inventory, automation, cross-docking, and regular audits, wholesalers can streamline their inventory management processes and achieve significant benefits. Implementing advanced technologies, training employees, and continuously monitoring performance are crucial steps in maintaining efficient and effective inventory management. As the market landscape continues to evolve, staying proactive and adaptable will ensure long-term success and competitiveness in the wholesale industry.