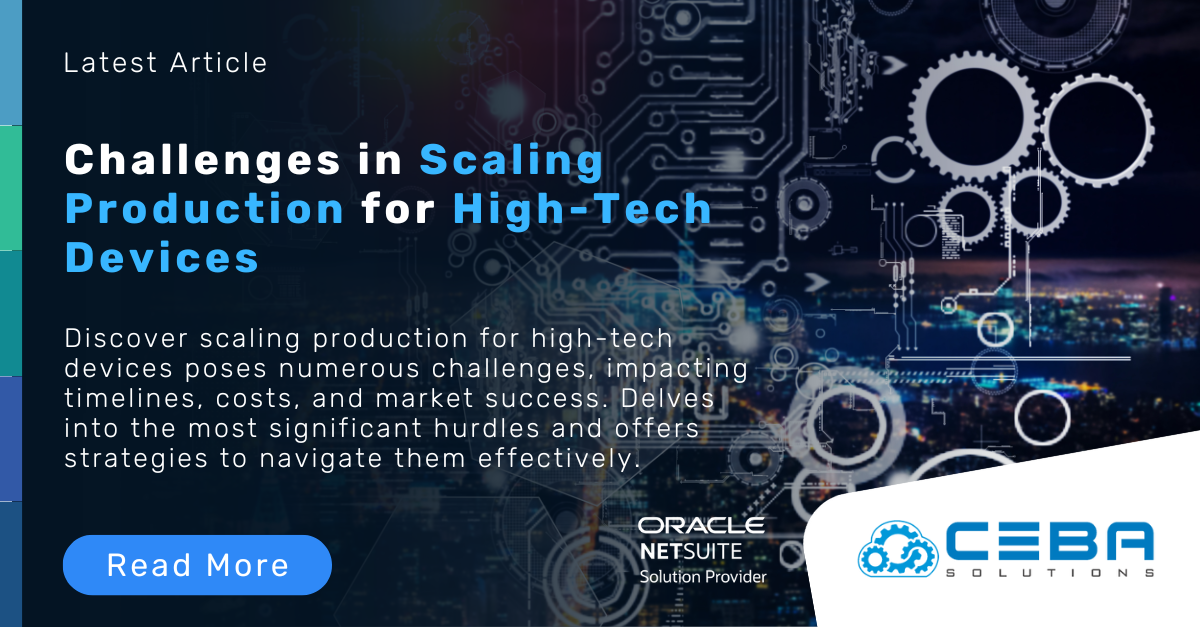
Challenges in Scaling Production for High-Tech Devices
Challenges in Scaling Production for High-Tech Devices
The rapid advancement of technology and the increasing demand for high-tech devices such as smartphones, laptops, wearables, and advanced medical equipment have placed immense pressure on manufacturers to scale production efficiently. Scaling production for high-tech devices involves more than just increasing output; it requires managing complex processes, ensuring quality, and adapting to fast-changing market demands. This article explores the significant challenges manufacturers face in scaling production for high-tech devices and discusses strategies to overcome these hurdles.
Key Challenges in Scaling Production for High-Tech Devices
- Supply Chain Complexity and Dependency
- Component Shortages: The production of high-tech devices relies heavily on a complex supply chain of specialized components, such as semiconductors, memory chips, and sensors. Disruptions in the supply chain, such as the global semiconductor shortage, can severely impact production timelines and costs.
- Supplier Dependence: High dependency on a limited number of suppliers for critical components can lead to bottlenecks. Any disruption at a key supplier's facility, whether due to natural disasters, geopolitical tensions, or logistical issues, can halt production.
- Maintaining Quality and Consistency
- Stringent Quality Standards: High-tech devices require precision manufacturing to meet stringent quality and performance standards. Scaling production while maintaining these standards can be challenging, as increased volume often leads to variability and potential quality issues.
- Defect Detection: As production scales, the ability to detect and address defects in real-time becomes more critical. Ensuring that each unit meets the required specifications without significantly increasing inspection time and cost is a major challenge.
- Technological Advancements and Upgrades
- Rapid Innovation Cycles: The high-tech industry is characterized by rapid innovation cycles. Manufacturers must continuously upgrade their processes and equipment to accommodate new technologies, which can be both time-consuming and costly.
- Integration of New Technologies: Integrating new technologies into existing production lines can be complex and may require significant modifications to processes and equipment.
- Workforce Skills and Training
- Skilled Labor Shortages: High-tech manufacturing requires a workforce with specialized skills and knowledge. Finding and retaining skilled labor can be difficult, particularly in regions with high demand for technical expertise.
- Continuous Training: As new technologies and processes are introduced, continuous training and upskilling of the workforce are necessary to maintain productivity and quality.
- Regulatory Compliance and Standards
- Complex Regulations: High-tech devices often need to comply with a range of regulatory standards, which can vary by region. Ensuring compliance while scaling production adds complexity and requires robust quality management systems.
- Environmental and Safety Standards: Meeting stringent environmental and safety standards is essential, and scaling production must not compromise compliance with these regulations.
- Cost Management
- Capital Expenditure: Scaling production typically involves significant capital investment in new equipment, facilities, and technologies. Managing these costs while maintaining profitability is a critical challenge.
- Operational Costs: Increased production volume can lead to higher operational costs, including labor, materials, and energy. Efficiently managing these costs is essential to ensure competitiveness.
Strategies to Overcome Production Scaling Challenges
- Supply Chain Diversification and Resilience
- Multi-Sourcing: Develop a multi-sourcing strategy to reduce dependency on single suppliers for critical components. Diversifying the supplier base enhances resilience and reduces the risk of supply chain disruptions.
- Local Sourcing: Consider sourcing components locally or regionally to reduce transportation risks and lead times. Local sourcing can also provide greater control over supply chain logistics.
- Investing in Advanced Manufacturing Technologies
- Automation and Robotics: Invest in automation and robotics to enhance production efficiency, reduce variability, and maintain high quality. Automated systems can handle repetitive tasks with precision and speed, improving overall productivity.
- Advanced Quality Control: Implement advanced quality control technologies, such as AI-powered inspection systems and real-time monitoring, to detect and address defects early in the production process.
- Adopting Agile Manufacturing Practices
- Flexible Production Lines: Design flexible production lines that can be quickly reconfigured to accommodate different products or changes in demand. Agile manufacturing practices enable faster response to market changes and technological advancements.
- Modular Manufacturing: Utilize modular manufacturing techniques to allow for easier integration of new technologies and processes. Modular systems can be scaled up or down as needed, providing greater flexibility.
- Enhancing Workforce Skills and Capabilities
- Training Programs: Develop comprehensive training programs to upskill the workforce in new technologies and processes. Continuous learning and development ensure that employees remain proficient and productive.
- Talent Acquisition: Implement strategies to attract and retain skilled talent, such as offering competitive compensation, career development opportunities, and a positive work environment.
- Strengthening Regulatory Compliance Systems
- Robust Quality Management: Establish robust quality management systems that ensure compliance with regulatory standards and enable efficient scaling of production. Regular audits and continuous improvement practices help maintain high standards.
- Environmental and Safety Initiatives: Invest in initiatives that enhance environmental sustainability and safety compliance. Implementing green manufacturing practices can reduce environmental impact and meet regulatory requirements.
- Effective Cost Management
- Lean Manufacturing: Adopt lean manufacturing principles to eliminate waste, optimize resource use, and reduce operational costs. Lean practices improve efficiency and productivity, supporting sustainable scaling.
- Cost-Benefit Analysis: Conduct thorough cost-benefit analyses for capital investments and operational changes. Strategic investments in technology and process improvements can yield long-term savings and competitive advantages.
Conclusion
Scaling production for high-tech devices presents a complex set of challenges that require careful planning, strategic investments, and continuous innovation. By addressing supply chain dependencies, maintaining quality standards, integrating new technologies, enhancing workforce capabilities, ensuring regulatory compliance, and managing costs effectively, manufacturers can successfully scale their production operations. Embracing advanced manufacturing technologies, agile practices, and sustainable initiatives will be key to overcoming these challenges and maintaining competitiveness in the fast-paced high-tech industry. As the demand for high-tech devices continues to grow, manufacturers that prioritize efficiency, quality, and resilience will be well-positioned to thrive in the evolving market landscape.